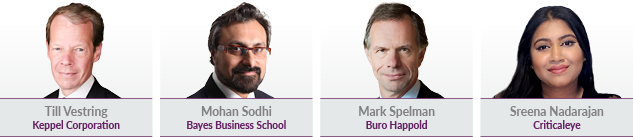
Global supply chains are facing the worst shortages in fifty years. A major confluence of factors, such as the bounce-back in consumer demand, rocketing inflation, and geopolitical differences have come together and overwhelmed traditional systems of delivery and logistics.
The disruptions could knock 4 percent to 5 percent off industrial production in the next year or two, according to the World Economic Forum (WEF). Since the summer of 2021, supply problems have led to delayed deliveries, soaring prices, gaps on supermarket shelves and empty petrol stations.
Challenges are both global, regional and local. In the UK, for example, a survey from the Confederation of British Industry (CBI) found that business stock levels were at their lowest levels since 1983, while an ONS (Office for National Statistics) survey estimated that 23 percent of firms in the UK could not get the goods and services they needed from the EU, while 15 percent could not get them from within the UK.
Sreena Nadarajan, Head of Research (UK) at Criticaleye, comments: “Boards need to ask whether their supply chain models are fit-for-purpose in a volatile business landscape. For a long time, there has been talk about agility in the supply chain, but now it’s a case of making it happen in a way that’s both sustainable and cost-effective.”
It is easier said than done, especially given the problem of inflated pricing and cost structures. So, what does this all mean for senior business leaders? Are these short-term pressures, or are we witnessing a more fundamental shift in how goods and services are delivered?
We spoke to Members of the Criticaleye Community to get their views on the underlying reasons for what’s happening in the supply chain.
This is what they had to say:
Till Vestring, Board Member, Keppel Corporation and Board Mentor, Criticaleye, says that geopolitics is forcing companies to rethink traditional approaches to logistics
It seems the frequency of the shocks to the supply chain have increased and the ripple effects they create are larger and take longer to subside. So, what looks like a relatively short, exogenous shock, may actually take a couple of years to unwind.
There are big structural changes in the emergence of a more bipolar geopolitical system between the West and China. If you’re in the manufacturing space, this is fundamental because so much of your supply chain probably comes from China. Going forward you can’t rely so exclusively on a country, such as China, for your supply chain anymore.
Identifying other countries is challenging. Ten-years ago people were saying what a great manufacturing hub India would be. It’s closer to Europe, it's got this huge workforce and the costs are lower, but there has been limited success… It remains very difficult to get planning permission and the logistics are just not in place, such as the road and rail infrastructure. In China by contrast, strong central planning enables things to happen much more efficiently and faster.
Nearshoring is somewhat exaggerated by the media. People underestimate how difficult it is to do and how long it will take to move significant amounts of production or sourcing closer to where you sell it. The other problem is that it's obviously going to be more costly and, in a recessionary environment, companies are not going to want to raise prices too quickly. There are risks to nearshoring and it brings us back to this idea of needing diversified supply routes.
You've got to plan and be fit for purpose. You must get the right products to your customers in time, at the required quality, and at a competitive cost. You then need resilience, which essentially means where and how much buffer stock you keep, and how you diversify from single sourcing or dual sourcing to multiple suppliers in multiple locations. The next area to focus on is agility and building that into your system as you will not be able to predict what's going to go wrong. When it does, you will have to quickly shift volumes from one site to another. Increasingly, this is getting organisations to think about how they can work with partners in their ecosystem to adjust.
For me, sustainability is still one of the core issues. It comes in two flavours: one is environmental and specifically figuring out what is the carbon footprint of your supply chain, and how you reduce it; the second is around labour and the social part of ESG [Environmental, Social, Governance]. Traceability, standards and verification are important, and companies realise that the cost of messing up is very high.
Mohan Sodhi, Professor of Supply Chain Management, Bayes Business School, argues that companies need to get better at collaboration and partnerships
The increase in demand after the pandemic was obviously a good thing, but the supply chain just wasn’t ready. We saw shifts in demand, such as from cars to electronics, and that resulted in chip shortages that are continuing and may go on for yet another year.
We have also seen a shift occur during the pandemic from a ‘just-in-time’ mindset to one of holding a ‘just-in-case’ inventory due to shortages. Companies are over-ordering... and these inflated orders are adding to the disruption and shortages we’re seeing.
Supply chains are geographically well-spread and complex, and I think they’re only going to spread more over time as companies broaden their supply base. The idea that more things should be made locally, on the scale we’re discussing, is nice for political conversations and elections, but the reality is that for many industries, raw materials, components, and finished goods have to be sourced from different parts of the world.
You can talk about sustainability all day long – it certainly feels nice to do that, [publishing] a glossy sustainability report. But, for many companies, sustainability is not a top priority right now, given all the shortages of components and labour. Sure, it should be… but, right now, companies are more worried about their [own] survival and then comes their profits. Planet survival doesn’t figure into the list of top priorities.
One of the ways to mitigate risk is to become better at collaborating and forming partnerships with companies from other sectors and even competitors. For me, it’s the idea of creating ‘Commons’ at three levels: within the organisation across product lines; within a geographical region or sector with other companies; and within the country as a whole.
Firstly, the company can look at how resources are shared, including component commonality or information, across different product lines of a company. Secondly, the company can work with competitors and other companies to create efficiencies through shared resources such as warehouse space and distribution. That way, all companies get more capacity overall in case any of them gets a demand surge. Finally, having ‘Commons’ at a country level means shared infrastructure or capacity across sectors as, for instance, we are seeing the US offer huge subsidies to companies to set up chip manufacturing in the US.
Firstly, the company can look at how resources are shared, including component commonality or information, across different product lines of a company. Secondly, the company can work with competitors and other companies to create efficiencies through shared resources such as warehouse space and distribution. That way, all companies get more capacity overall in case any of them gets a demand surge. Finally, having ‘Commons’ at a country level means shared infrastructure or capacity across sectors as, for instance, we are seeing the US offer huge subsidies to companies to set up chip manufacturing in the US.
Overcoming the kind of systemic disruption we’re seeing now requires a change in the mindset and the business model that must be driven by the Board looking long term into the future.
Mark Spelman, Non-executive Director, Buro Happold and Board Mentor, Criticaleye, highlights the importance of sustainability and technology in transforming how we approach supply and demand
Supply chains are fundamentally changing. It is too simplistic to suggest this is just about the pandemic or even geo-politics. There are a number of fundamental factors at work, remodelling supply chains from climate to new technologies and the circular economy.
Technology is a key driver of change. The rollout of 5G will be hugely significant, especially as it accelerates the growth of the IoT [Internet of Things]. The issues around climate change extend beyond decarbonisation as can be seen by how extreme weather events impact investment decisions on the locations of factories and logistics. For example, in Australia the long-term impact of fires and floods is a major investment criteria.
Multiple trends are converging across geo-politics, environment, demographics and technology. Together, these forces are leading to a restructuring of supply chains – this is more than an anti-globalisation trend. The emphasis varies by industry and sector. For instance, transparency in fashion, recycling in electronics, and chips in automotive as cars increasingly become data platforms. Together, these challenges are producing significant disruption and the need to repurpose supply chain models.
The question of where products are sourced from will remain important. We are seeing a trend towards more distributed manufacturing, but that does not mean all products will be sourced locally… More and more products have embedded intelligence and so sourcing chips will be one of the key issues for this decade. It will not be solved any time soon by local sourcing, but by resilience embedded through global suppliers.
It seems to me that too much supply chain debate muddles what should happen globally, regionally, and locally.
To mitigate risk, companies will need to have a robust data architecture in the supply chain, especially when on average 87% of an organisation’s carbon emissions are outside its direct control. Going forward, businesses will need to use artificial intelligence, automation, and digital twins to optimise supply-chain tracking and measurement.
From a Board perspective, they will need to understand how management is combining innovation, resilience and efficiency in building supply chains of the future.
Arya Ghassemi, Content, Criticaleye